Five-axis machining technology in precision machining has been the bulk of the demand for industrial areas, can practice high-end CNC tooling machines and moulds of key equipment. The quality level of mould products to a large extent by the influence of CNC equipment, in the highly competitive market environment, the manufacturing industry is facing the challenge of seeking shorter production cycle, higher processing quality, more rapid product re-modelling and processing capabilities, as well as lower manufacturing costs, and therefore five-axis machining technology is also therefore highly valued. In this article, we will discuss the principles and application of 5-axis machining technology to help you more easily understand how to introduce 5-axis machining technology to bring transformation opportunities for enterprises.
What is 5-axis machining? Principles of operation, advantages of understanding at a time.
Five-axis machining is an advanced CNC machine tool machining technology, which can simultaneously control the movement of the workpiece in the X, Y and Z linear axes as well as the A and B rotary axes. This technology offers a high degree of flexibility and precision, allowing us to implement the production of parts with high complexity and stringent precision requirements.
Principle of operation
When cutting metal, the huge cutting and friction forces can cause the workpiece to move, so "one axis" is needed to hold the workpiece in place. The common three-axis tooling machine has only three degrees of freedom for linear movement and can handle structures along the tool axis, but cannot handle side structure features. Five-axis machining is the use of at least five coordinate axes (X, Y, Z, A, B, three linear coordinates and two rotary coordinates) under the co-ordinated control of a computer numerical control (CNC) system, so that each axis has an independent controller and a motor drive system to carry out simultaneous motion machining.
Five-axis machining is also divided into real five-axis and fake five-axis?
Sometimes what you think is 5-axis is not really 5-axis! True 5-axis machining technology must have RTCP (Rotational Tool Center Point) functionality; that is, the ability of the machine tool to keep the cutting point of the tool (the tool‘s centre point) unchanged during simultaneous 5-axis movement, even if the tool itself is rotating or tilting. So how can you tell? The easiest way is to see if the axes are moving at the same time! True 5-axis means 5-axis 5-linkage, while false 5-axis may be 5-axis 3-linkage, the other two axes only play a positioning function.
Advantages of 5-axis machining
Ability to machine complex geometries: 5-axis machining technology allows for the machining of multiple surfaces in a single setup, avoiding the errors associated with multiple fixture changes.
Increased productivity: 5-axis machining reduces the number of stops and fixture changes during the machining process, thereby increasing productivity.
Shorten production cycles: 5-axis machining can shorten the entire production cycle by reducing set-up times during machining.
Improved machining accuracy: 5-axis machining technology can also improve machining accuracy due to the reduction of errors in machining.
Extended tool life: During 5-axis machining, the tool has a smaller contact area with the workpiece, which helps to reduce the rate of tool wear and extend tool life.
The above is a detailed introduction to CNC five-axis machining, I hope to give you a clearer understanding of five-axis machining related knowledge.
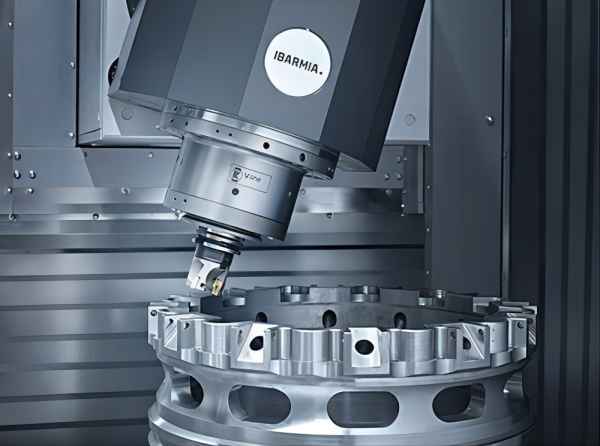